FINITE ELEMENT ANALYSIS (FEA)
Validate, guide and optimize your design at a lower cost
Finite element analysis : a longstanding expertise at inoprod
The Finite Element Method (FEM) is a numerical approach to simulate the physical behavior of a simple component to a complex system. The integration of an advanced definition of contacts, materials, boundary conditions and loads, coupled with the use of standards and regulations, makes possible the implementation of finite element models that are as faithful as possible to reality. Inoprod’s longstanding expertise, mechanical dimensioning and optimization, is an integral part of the company’s approach, which consists in accompanying its customers towards Industry 4.0.
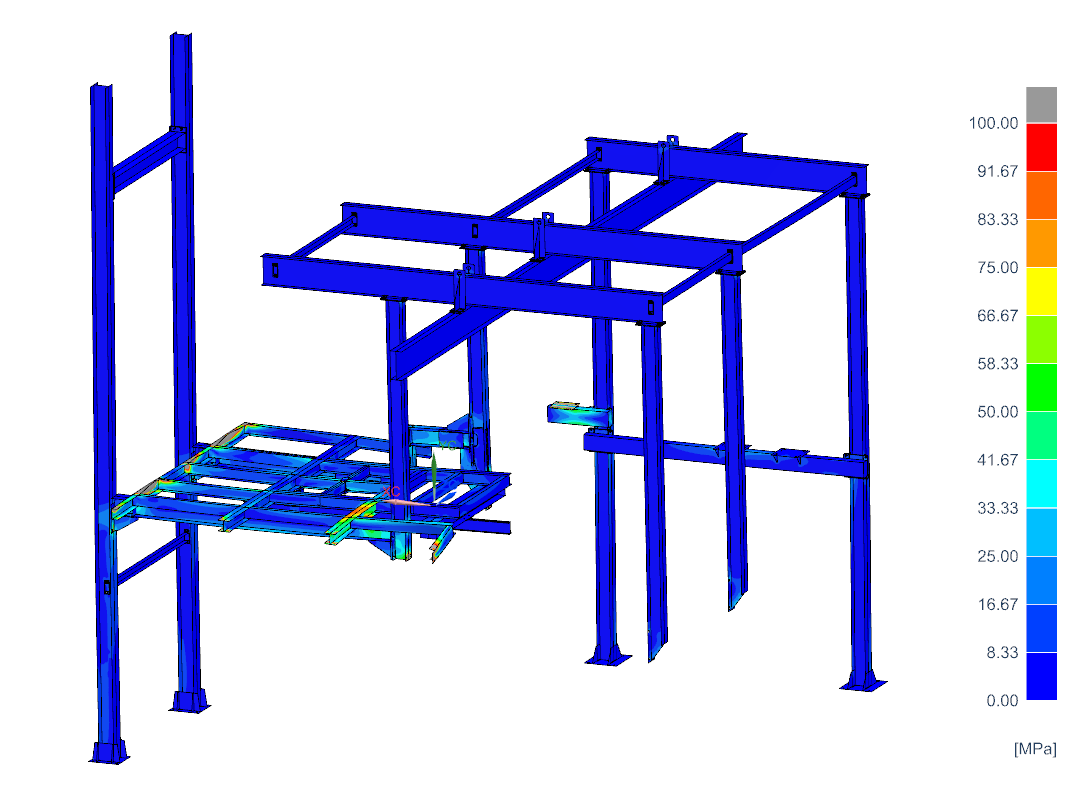
Validate, guide or optimize your design at a lower cost through the finite element method
Through numerical simulation
A finite element model reproduces the geometry of your system, integrating all parts involved in its mechanical operation. The different materials are taken into account through constitutive equations. Loads are simulated in an isolated or simultaneous way, according to your specifications or normative criteria, in order to analyze the impacts. Based on materials criteria or stress limits, parts and assembly elements are analyzed and Inoprod proposes improvement solutions if necessary.
At each phase of product’s life cycle
Pre-dimensioning
During the design of a new product, a component and system pre-dimensioning allows to characterize its behavior in relation to its future environment, to guide and optimize the geometrical definition, to select materials, to validate the service lifetime and to meet normative requirements.
Design validation
Products validation phases prior to manufacturing release can also be carried out in order to secure investments.
Product evolution
Equipment evolution, during their utilization phases, may also require a finite element analysis in order to integrate the new loads and the possible new normative constraints, and to ensure the mechanical resistance of the equipment while defining the necessary reinforcements.
Dismantling
At the end of the equipment’s life, it is also necessary to verify the elements necessary for dismantling in order to ensure the safety of the people involved.
Our experts in numerical simulation support you in the realization of your analysis
Kinds of calculations we can carry out
Static :
- Linear
- Non-linear (contact, materials)
- Buckling
- Pressurized equipment
- Transmission (coupling, bearing, power, gears)
Dynamics :
- Transient
Fast dynamics :
- Crash
- Impact
- Energy absorption
- Predictive breaking
Vibratory :
- Modal analysis
- Seismic
- Harmonic
- Random
Thermal :
- Stationary
- Transitional
Optimization :
- Parametric
- Topological
Material's types
- Isotropic
- Orthotropic
- Anisotropic
- Hyper-elastic
- Viscoelasticity, Viscoplasticity
- Residual deformation (Bergström-Boyce)
- Composite material
- Material behaviour based on experimental data
Our software solutions
Most of our finite element calculations are performed with reference solutions such as NX Simcenter and Ansys. Our team is also trained to use other tools such as Altair.
They trust us
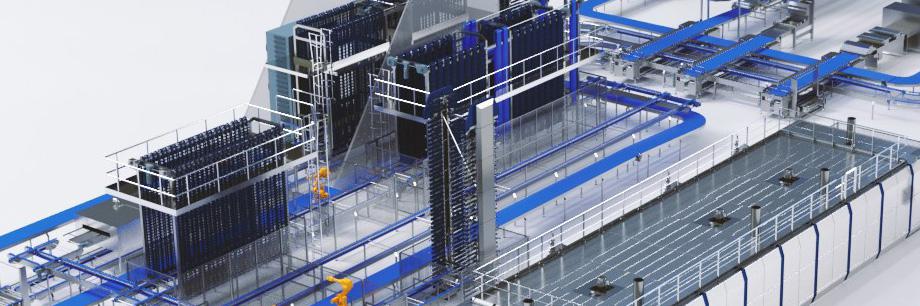
Mecatherm
More flexible and efficient production lines with Tecnomatix® Plant Simulation.
Learn more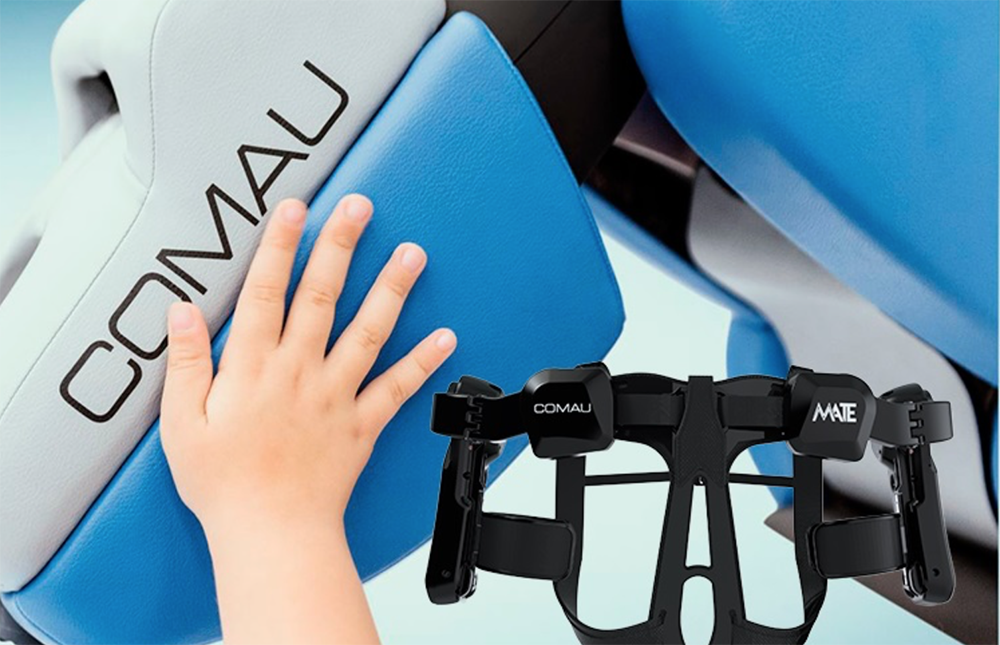
Comau
Securing the production and performance of a production line by a dynamic simulation
Learn more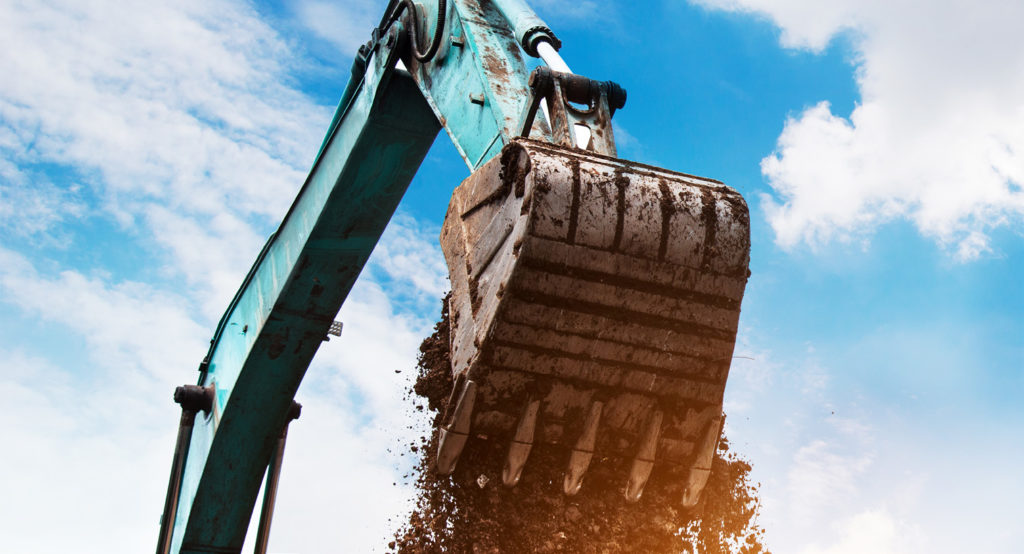
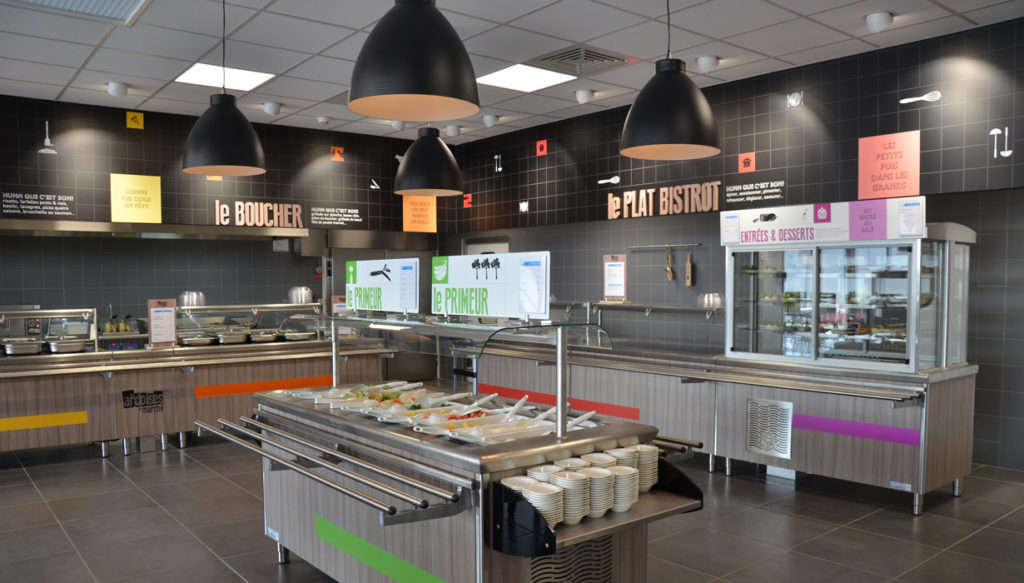